Unlock Precision in Thin Film Coating
3 Key Strategies for Research Labs
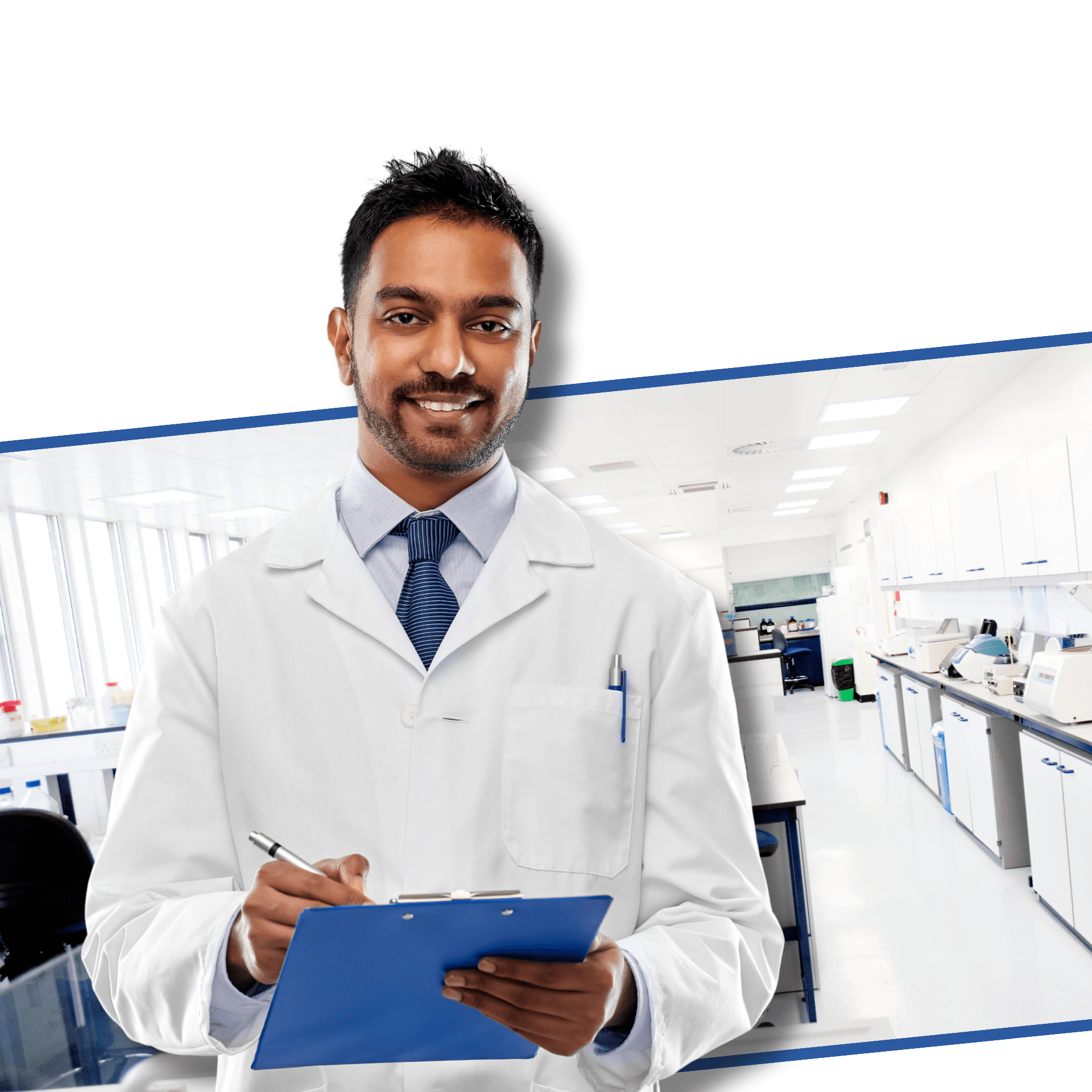
You’re likely here because you’re facing the same thin-film coating challenges as many other research teams – inconsistent results, wasted time, and the constant need to optimize your processes – isn’t it? As you know, recent research shows that over 40% of labs struggle with thin-film reproducibility, significantly impacting research outcomes (Source: Journal of Materials Science, 2024). And poor quality thin-film coatings can also cause a 20-30% reduction in overall research efficiency (Source: Nanotechnology Research Insights, 2024). But what if you could consistently achieve precision and reliability, where smart spin coating machines are the problem solvers, and have been designed with the goal that high quality research starts with high quality coatings.
In this brief guide, we’ll share three key strategies that can help you enhance your thin-film coating results, and demonstrate how modern spin coaters are specifically designed to address these challenges.
Strategy 1: Optimize Your Solution Properties
Research reports and industry experts say that the properties of your coating solution significantly affect the outcome, so here’s what you should consider:
- Viscosity Control: High-viscosity solutions are notorious for causing non-uniformity, thus consider diluting your solution with a compatible solvent to improve its spread-ability.
- Surface Tension: Adjustments to the surface tension of the coating solution can help with substrate wetting and a more even distribution.
- Dispensing Parameters: Experiment with low dispense rates and volumes to achieve better control over the initial coating process.
How Spin Coaters Help:
The spin coating machines feature a center hole in the lid for precise liquid dispensing, allowing you to fine-tune your dispense rate and volume. The NT12000 has a non-vacuum substrate holding mechanism too (PATENT PENDING) for unique applications.
Strategy 2: Master Your Spin Parameters
Inputs from research forums indicate that proper spin parameters are critical for achieving the desired coating thickness and uniformity, hence you can follow these suggestions after consulting the brand representatives:
- Multi-Step Spin Process: Start with a lower spin speed for the initial coating phase to allow for an even distribution, followed by higher speeds for solvent removal.
- Acceleration: Use controlled acceleration parameters to avoid edge effects.
- Spin Duration: Adjust the spin time to ensure a smooth and even coating with no excess material.
How Spin Coaters Help:
- The spin coaters offer programmable spin speed, spin duration, and spin acceleration, allowing for complex, multi-step spin profiles. Their machines feature an acceleration of up to 8000 RPM/s and a maximum speed of 12000 RPM, giving you the power to fully explore new applications and materials. The live RPM vs TIME graph on both machines also provides critical information about the coating process.
- The NT12000 offers a speed accuracy of ±1%, ensuring reproducible results.
Strategy 3: Prioritize Substrate Preparation
Here it is about the importance of a clean and properly prepared substrate that is essential for optimal coating results, so you need to ensure:
- Cleanliness: That the substrate is completely free of contaminants by using an appropriate cleaning solution and equipment.
- Adhesion: Selection of an appropriate chuck to securely hold the substrate and provide consistent results.
- Surface Treatments: Consider chemical or plasma treatments to enhance the surface adhesion properties for your selected material.
How Spin Coaters Help:
- Both the NT12000 and NTCR8 offer a universal vacuum chuck and a hybrid vacuum/vacuum-less holding mechanism, providing versatility for various substrate sizes and materials, from 1 inch to 9 inch. The NTCR8 also includes 3 vacuum chucks to accommodate different sizes. The ability to use a vacuum chuck or vacuum-less holding makes them useful for a wide variety of research applications.
- Both systems include a nitrogen purging connection to provide environmental control during the coating process.
Why Choose Navson Technologies’ Spin Coaters for Thin Film Coating?
The NT website says they provide you with the ability to control your thin film parameters for consistent, reproducible results. Their NT12000 and NTCR8 spin coaters are designed for precision and flexibility, and are engineered to provide high quality coatings with minimal effort. Their 7 inch touch screen interface makes programing, operation and data analysis simple and easy, a necessity for all nanotechnology research projects.
But you don’t have to just take our word for it, see how the NT12000 has helped this team:
Improving your thin-film coating process doesn’t have to be an uphill battle as per the above considerations. By optimizing your solution properties, mastering your spin parameters, and prioritizing substrate preparation, combined with the precision and versatility of the modern spin coaters, you can achieve reliable and repeatable results, and take your research to the next level.
Ready to achieve precision in your research?
Click below to speak to a Navson Technologies expert. Discuss your unique coating challenges and identify how the NT spin coaters can help you achieve your goals.
Disclaimer:
The information in this article is for informational and educational purposes only. It is not medical or scientific advice and should not replace professional consultation, diagnosis, or treatment. We make no guarantees about the accuracy or reliability of the information. References to research studies are for illustrative purposes and should not be seen as endorsements. We are not responsible for any loss or damage from using this information.