Building Nanomaterials with Precision and Control
Do you ever imagine a world where materials are crafted on an nanoscale, designed for specific purposes with incredible efficiency? Well then, you must be one of the many researchers who are working on sol-gel method that is revolutionizing nanomaterial synthesis, offering a powerful tool to build a brighter future.
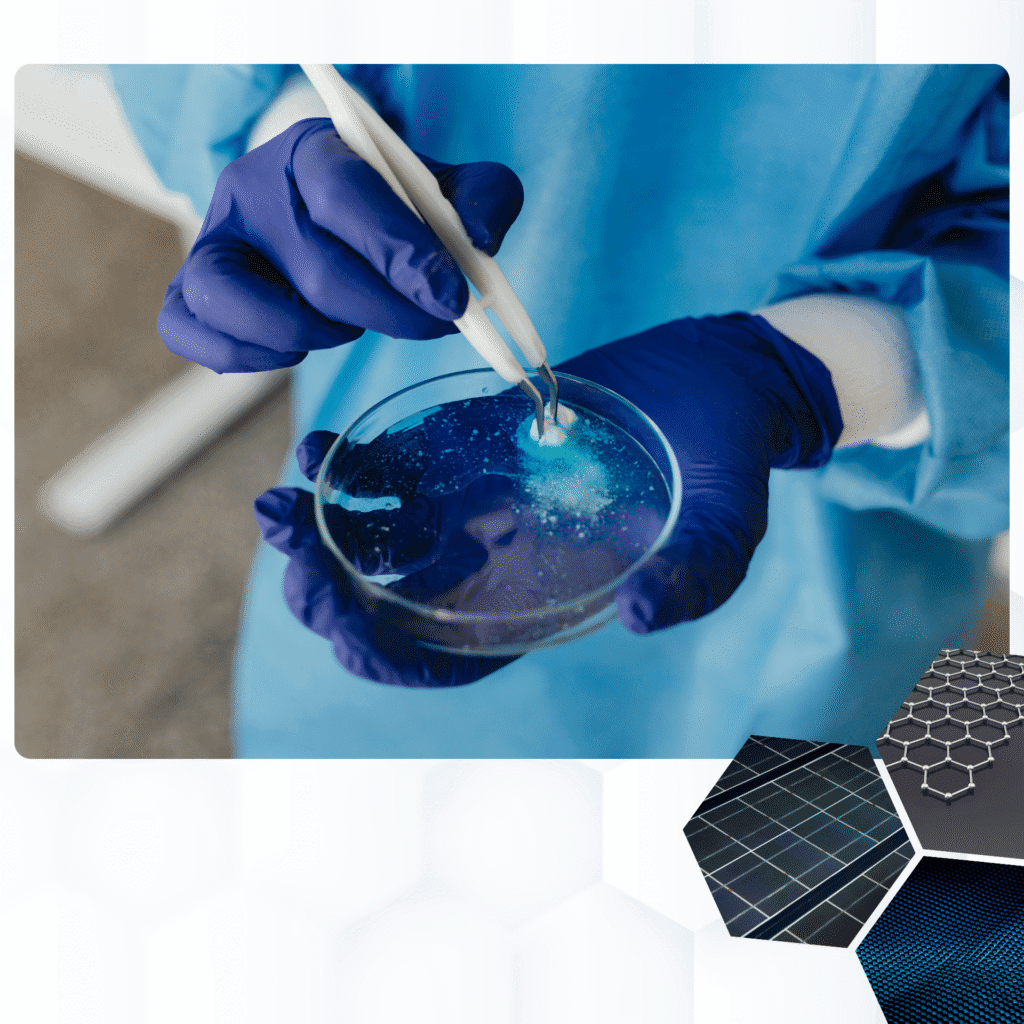
In this post let’s explore the motive behind this method, it’s various applications, among other parameters.
Why Sol-Gel Method?
If you are new to this, you can think of sol-gel method as an expert’s recipe for fabrication of nanomaterials. So it starts with the expert carefully selecting ingredients (precursors) and controlling the cooking process (hydrolysis and condensation), that can help create a stunning variety of nanoparticles with unique properties. This precise control allows for:
- The designing of materials that are super strong yet lightweight, that can conduct electricity efficiently while remaining transparent!
- The sol-gel technique often operates at lower temperatures and uses less harsh chemicals compared to traditional techniques that opens doors for greener nanomaterial production.
- From catalysts for clean energy production to drug delivery systems in medicine, sol-gel process paves the way for innovation across countless fields.
Sol-Gel for a Brighter Tomorrow
In this 21st century, Nanotechnology holds immense potential, but responsible development will be the key to a better world. Here Sol-gel technique, with its emphasis on control and precision, is empowering scientists and researchers to explore the development of materials with a focus on safety and positive impact on the world. As fellow humans, we can expect more collaborations across disciplines and open knowledge sharing to leverage the power of sol-gel to develop nanomaterials that solve real-world challenges and improve our lives.
Sol Gel Method Applications
If you have been working on the sol-gel method, you may agree that it unfolds like a painter’s magic, transforming liquid precursors into a dazzling array of functional materials. That’s the reason why researchers are using it to sculpt delicate, feather-light aerogels for superior insulation to razor-sharp nanoparticles for targeted drug delivery, at the nano level. Imagine how this method can be use to craft windows coated with invisible thin films for self-cleaning or energy-saving purposes, or intricate biosensors that detect diseases with unmatched precision – all highlighting the elegance of this versatile technique.
Here is a quick comparison on the challenges and limitations of sol-gel method vs spin coating method vs spray pyrolysis method:
Method | Challenges | Limitations |
Sol-Gel | Multi-step process: Requires careful control over each step (hydrolysis, condensation, etc.) for desired properties. Slow drying times: Can lead to cracking or inhomogeneity in films. Limited precursor availability: Not all materials have readily available sol-gel precursors. | Difficulty achieving highly uniform films on large substrates. Requires post-deposition heat treatment: May not be suitable for temperature-sensitive materials. |
Spin Coating | Limited film thickness control: Difficult to achieve very thick films. Requires a flat and smooth substrate: Not suitable for complex geometries. High solvent consumption: Can be environmentally unfriendly. | Not ideal for depositing highly viscous solutions. May suffer from edge effects: Film thickness can be non-uniform at the edges of the substrate. |
Spray Pyrolysis | Poor control over film stoichiometry: Difficult to achieve precise chemical composition. Potential for particle agglomeration: Can lead to rough and inhomogeneous films. Safety concerns: Requires handling of flammable precursors and high temperatures. | Limited control over film morphology: Difficult to achieve highly oriented or textured films. Not suitable for depositing on heat-sensitive substrates. |
As can be seen from the above points, the sol-gel method reigns supreme for its versatility and control, but alternative methods can be used for specific needs. Like for large-scale, rapid deposition, spray coating offers a faster and potentially more cost-effective approach. Then you have the physical vapor deposition (PVD) techniques like sputtering and evaporation that provide excellent control over film composition and thickness, particularly for high-quality electronic materials. Or the electrochemical deposition process that allows for site-specific and patterned growth, desirable for microelectronics applications. Ultimately, the choice of method hinges on the desired material properties, production scale, and cost considerations, isn’t it?
Ready to simplify your spin coater procurement?
At Scientific EQ, we provide unbiased, expert guidance to help Indian labs compare quotes fairly, avoid regretful purchases, and speed up the sourcing process. You can start with these free resources that are designed to make you feel confident, not confused:
- 🔍 Spin Coater Pre-Purchase Checklist
- 🔬 Spin Coating Process Optimization Guide
- 🧰 Basic Maintenance Toolkit
- 📅 Free Expert Call (Optional — not sales)
Free Sourcing Call + Spin Coater Sourcing Toolkit: Start Now📥
Free Sourcing Call
Completely Confidential – Speak directly with product experts. We’ll email a pre-purchase checklist and bonus toolkit for your reference.
About Scientific EQ
We’re not a manufacturer or a supplier. We may earn from affiliate commissions if you buy products linked from our website. Scientific EQ is a neutral team that helps researchers, procurement heads, and PhDs:
- Compare quotes fairly
- Avoid regretful purchases
- Speed up the sourcing process
- Focus on research, not chasing suppliers
We help you focus on research, not chasing suppliers. Because in research, what you don’t buy matters just as much as what you do.
We’re here to reduce confusion, not create it.
Important Disclaimer
This site offers general information and best practices for spin coating applications. It is not intended as a substitute for professional training, specific equipment operation manuals, or a comprehensive understanding of the materials involved. Users bear sole responsibility for ensuring safe operation, appropriate material selection, and adherence to all relevant safety and environmental regulations.
Should you identify any discrepancies or have questions regarding the content of this guide, please contact us promptly at scientificeq@aidasinc.com. We are committed to rectifying any inaccuracies and will gladly acknowledge contributing sources.